1 技术融合的必然趋势
农业机械化正经历着从传统动力向新能源、智能化方向的深刻变革。混合动力系统作为传统燃油动力向纯电过渡的关键技术路线,在拖拉机领域展现出巨大潜力。而双离合器变速箱技术(Dual Clutch Transmission, DCT)凭借其高效率传动、无动力中断换挡等优势,正成为混合动力拖拉机动力系统的理想选择。这一技术融合不仅能够解决传统拖拉机作业中存在的高排放、高油耗、操作复杂等痛点,还能有效适应不同作业场景下对动力输出的多样化需求。随着全球农机行业向“绿色智能”方向加速转型,双离合器技术在混合动力拖拉机中的应用已成为推动农业机械升级的重要技术路径。
2 技术原理与系统构型创新
双离合器变速箱技术通过两套独立离合器的协同工作,实现了动力传递的无缝衔接与高效转换。其核心工作原理在于:当奇数挡位处于工作状态时,偶数挡位的相邻齿轮已完成预啮合准备;换挡时只需切换离合器状态,即可实现挡位间的瞬时切换。这一技术特性使拖拉机在复杂作业环境中能够保持连续动力输出,避免因换挡导致的作业中断,特别适合耕作、播种等需要稳定牵引力的作业场景。
在混合动力拖拉机中,双离合器变速箱与电机系统的融合催生了多种创新构型:
三种驱动模式:混合动力拖拉机采用双离合器变速箱后,可实现纯电驱动(EV)、混合驱动和发动机驱动三种作业模式的灵活切换。当拖拉机进行轻载作业且行驶速度不高时,可单独由电机驱动,实现零排放运行;当拖拉机在重载、中载挡位工作且需求功率大时,发动机和电机可同时驱动拖拉机行驶作业;而当拖拉机处于运输挡位工作且需求功率适宜时,发动机在提供作业功率的同时还能为电机提供额外发电功率,实现能量回收利用。
行星齿轮耦合系统:先进的混合动力拖拉机采用行星齿轮机构作为动力耦合装置,其太阳轮与双离合器变速箱的实心输入轴相连,内齿圈与减速电机的输出轴相连,而行星轮则与变速箱的重载二挡齿轮副相连。这种构型实现了发动机动力与电机动力的高效耦合与分流,使系统能够根据作业负荷自动优化动力源组合。
多挡位专业化设计:针对拖拉机特殊作业需求,双离合器变速箱设置了多级专用挡位,包括重载挡、中载挡和运输挡等。这些挡位按传动比大小排列,通过同步器实现挡位切换。如重载一挡齿轮副与运输一挡齿轮副成对排列,二者之间设有专用同步器;运输一挡齿轮副与中载一挡齿轮副之间同样设有同步器。这种设计确保了拖拉机在各种作业条件下都能匹配最佳传动比。
表1:混合动力拖拉机双离合器变速箱的挡位配置与功能
挡位类型 | 适用场景 | 扭矩范围 | 作业特点 | 动力源组合 |
重载挡 | 深耕、开荒等 | 高扭矩 | 低速大扭矩 | 发动机+电机混合 |
中载挡 | 旋耕、播种等 | 中扭矩 | 均衡作业 | 发动机为主/混合 |
运输挡 | 田间运输 | 低扭矩 | 高速低耗 | 发动机驱动+充电 |
轻载挡 | 轻质土壤作业 | 较低扭矩 | 高效节能 | 纯电驱动为主 |
3.技术挑战与解决方案
尽管双离合器变速箱技术在混合动力拖拉机中展现出巨大潜力,但在实际应用中仍面临一系列技术挑战,需要从多维度进行攻关突破:
3.1 模式切换的动态协调控制
混合动力拖拉机在不同驱动模式间切换时,由于发动机与电机的动态响应特性存在显著差异,容易导致扭矩波动和冲击,影响作业平顺性。研究表明,在无优化控制策略的情况下,模式切换过程中的最大冲击度可达7.1 m/s³,严重影响驾乘体验和传动系统寿命。针对这一挑战,研究者提出了多阶段协同控制策略:
基于PID反馈的转矩控制:通过精确控制动力源的实际输出转矩,减小模式切换过程中的扭矩波动。研究显示,该方法可将冲击度降低至1.78 m/s³,降幅达74.9%。
发动机扭矩变化率限制:通过控制加速踏板开度变化率,限制发动机扭矩的突变,避免动力输出的大幅波动。
电机扭矩补偿技术:利用驱动电机扭矩响应快的优势,主动补偿发动机扭矩响应滞后,实现动力输出的平滑过渡。
江苏大学等机构针对液压机械联合变速器(HMCVT)混合动力拖拉机开发了离合器切换正时优化方法,通过正交实验范围分析优化模式切换质量。仿真结果显示,该方法使输出轴速度下降幅度从17.647%降至6.591%,动态载荷系数从2.743降至1.857,切换时间从2.13秒缩短至1.71秒。这些控制技术的突破为双离合器在混合动力拖拉机中的稳定应用奠定了基础。
3.2 热管理与可靠性的提升
拖拉机在重负荷连续作业条件下,双离合器系统面临严峻的热负荷挑战。特别是在犁耕、深松等大阻力作业中,离合器频繁接合与滑摩会产生大量热量,导致温度急剧升高,不仅影响传动效率,还可能引发材料退化和系统失效。针对这一问题,行业提出了多层次解决方案:
高精度热管理模型与分级保护策略:构建离合器温度预测模型,实时监测热负荷状态,并实施分级保护控制。该策略在检测到温度接近临界值时主动调整扭矩分配,避免过热失效。
梯度涂层材料的应用:研发新型齿轮材料,通过表面处理工艺使齿轮表面硬度提升30%的同时保持芯部韧性,提高耐磨性和抗疲劳性。
集成化热管理系统:将润滑系统与冷却通道集成于壳体结构中,提升热管理效率40%。这种设计通过优化冷却液流动路径,增强关键部位的散热能力。
3.3 成本控制与产业化推广
混合动力拖拉机双离合器系统的高制造成本是目前制约其大规模应用的主要因素。与传统拖拉机相比,混合动力系统增加了电机、电池和复杂控制系统,导致初始投资大幅提高。为突破这一瓶颈,行业正在探索多种路径:
平台化与模块化设计:长安汽车等企业在双离合器开发中建立了“涵盖传统动力、48V系统、HEV/PHEV混合动力系统三大平台”的系列化产品体系,通过共享核心模块降低开发与制造成本。
智能制造技术应用:提升生产自动化率,如长安汽车建成的双离合器生产线自动化率达46.6%,大幅提高了生产效率和产品一致性。
本地化供应链建设:一拖股份等企业正在“加强产业链协同发展,通过提升自主研发能力、推动产业链上企业协同创新,加强关键核心零部件技术攻关,保障产业安全”,减少对进口部件的依赖。
4.4 丘陵山地适应性优化
中国丘陵山区约占国土面积的70%,这些地区对小型化、轻量化、高机动性农机具有迫切需求。传统大型拖拉机难以适应复杂地形,而双离合器变速箱与电驱动结合为小型智能农机开发提供了新思路。江西建摩新能源科技有限公司针对丘陵山区研发的X1纯电动微耕机系列、X1S轻量化微耕机、X2油电混合动力微耕机系列等产品,通过分布式农机换电站和共享农机模式,解决了“闲置率高、能源补给难、操作复杂”等实际问题4。未来双离合器技术在混合动力拖拉机中的应用需进一步向小型化、轻量化方向发展,以满足丘陵山地作业的特殊需求。
表2:混合动力拖拉机双离合器技术面临的主要挑战与解决方案
技术挑战 | 影响程度 | 关键技术对策 | 预期效果 | 研发进展 |
模式切换冲击 | 高(影响平顺性) | 多阶段协同控制策略 | 冲击度降低75% | 仿真验证阶段 |
热管理可靠性 | 高(持续作业能力) | 集成冷却+梯度材料 | 热管理效率提升40% | 实验室验证 |
系统成本 | 中(市场推广) | 平台化设计+自动化生产 | 制造成本降低30% | 初步应用 |
丘陵适应性 | 中(市场覆盖面) | 轻量化+模块化设计 | 重量减轻25% | 样机测试 |
控制系统复杂度 | 中(维护便利性) | 标准化接口+故障诊断 | 维护成本降低20% | 研发阶段 |
4应用前景与产业化路径
双离合器变速箱技术在混合动力拖拉机中的应用前景广阔,其产业化路径已初现端倪。结合技术发展趋势与市场需求,未来五年将迎来关键发展期。
4.1 政策与市场双重驱动
中国农机产业正处于转型升级的关键阶段。国家《中国制造2025》战略明确将双离合器变速箱(DCT)列为优先发展主题,旨在突破“由制造大国迈向制造强国”发展中的关键性卡脖子技术。一拖股份作为行业龙头,在《2025年“提质增效重回报”行动方案》中明确提出“加速推进大马力无级变速、动力换挡、混合动力等高端智能拖拉机的研发与熟化应用,形成可直接替代进口的产品和技术”。这些战略布局为双离合器技术在混合动力拖拉机中的应用提供了强有力的政策支持与资源保障。
市场端同样展现出强劲需求。随着农业规模化经营加速推进,大型农场和专业合作社对高效智能农机的需求快速增长。新疆试验活动中,英轩油电混动拖拉机在极端条件下的优异表现引发了行业高度关注,其“更绿色、更智能、更高效、更可靠”的技术特点代表了未来发展方向。这种市场认可将加速双离合器混合动力拖拉机的产业化进程。
4.2 技术路线演进趋势
双离合器技术在混合动力拖拉机中的应用将沿三条主线深化发展:
动力总成高度集成化:玉柴集团开发的YCK09和YCA05P等IE-Power混动电驱总成代表了“发动机与电机高度集成化设计”的最新趋势。未来产品将进一步整合双离合器变速箱、电机控制系统和能量管理系统,形成模块化动力单元,实现轴向尺寸压缩至传统方案的60%,为电池布局腾出空间。
控制算法智能化升级:基于数字孪生的预测性维护系统将实现寿命预测精度±5%1,大幅提升系统可靠性。同时,多传感器信息融合技术的应用将使控制系统能够实时感知作业负荷、地形条件和土壤状态,自动优化动力分配策略。一拖股份正在推进的“智能制造生产设备与工业互联信息技术深度融合应用”,为智能控制算法的发展提供了基础支撑。
能源管理策略优化:混合动力系统需要精细化的能量管理策略来最大化能效优势。YCF11-15kW增程器总成采用的“最优能量管理控制策略”实现了总成性能高度耦合,节油率高达25%~40%。未来能源管理将结合大数据与人工智能技术,根据作业历史、地形特征和作物类型预测能量需求,优化充放电策略。
4.3 产业化推进路径
双离合器混合动力拖拉机的产业化需分阶段稳步推进:
示范应用阶段(2025-2026):聚焦大型农场和国有农垦系统,开展小批量示范应用。重点验证系统在主要粮食产区不同工况下的适应性,积累运行数据。一拖股份计划“全力推进动力换向产品推广销售工作”2,为混合动力技术推广奠定市场基础。
技术完善阶段(2027-2028):针对示范应用中发现的问题进行技术优化,重点突破成本控制和大规模生产质量控制瓶颈。同时,“加强渠道建设和海外人才队伍建设,并针对不同国家和地区对农机产品的功能需求,加快出口型产品研发和适应性改进”,拓展国际市场。
大规模推广阶段(2029年后):形成涵盖“重载、中载、轻载、运输”全作业场景的产品系列,实现与传统拖拉机成本平价。建立覆盖全国的服务网络和备件供应链,为大规模市场推广提供保障。
5 结论
双离合器变速箱技术在混合动力拖拉机中的应用代表着农业机械传动系统的革命性进步。这一技术融合充分发挥了机械传动的高效可靠与电力驱动的灵活可控双重优势,为农业机械化发展注入新动能。其核心价值在于通过物理相位控制实现动力路径的智能重构,既保留了机械传动的可靠性本质,又赋予系统电子控制的灵活性特征1。
从产业化进程看,双离合器混合动力拖拉机已从技术验证阶段步入商业化应用初期。随着材料科学、控制算法与制造技术的协同进步,特别是梯度涂层材料、预测性维护系统和集成化热管理等技术的突破,双离合器变速箱在混合动力系统中的应用潜力将进一步释放。未来五年将是该技术规模化应用的关键期,需要产业链上下游协同创新,共同解决成本控制、热管理优化和丘陵适应性等技术挑战。
双离合器混合动力拖拉机的普及将对农业生产模式产生深远影响。它不仅能够显著降低燃油消耗和碳排放,还能通过提升作业精度和效率,为精准农业和智慧农业奠定装备基础。随着“双碳”战略在农业领域的深入推进,这一技术将成为农机装备升级的核心驱动力之一,引领农业机械走向高效、智能、绿色的新未来。
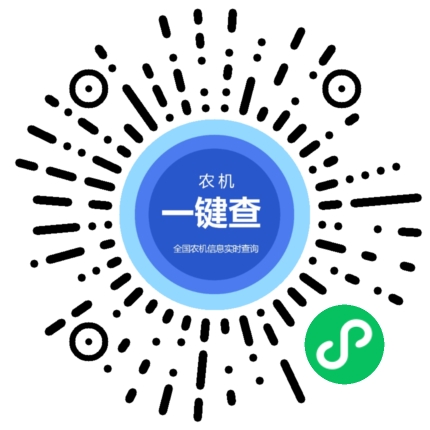
小程序扫码观看
更多农机资讯尽在农机一键查
版权声明:本文仅代表作者观点,不代表农机新闻网立场。 本文为分享行业信息所用,如需转载,请联系原作者。
网友评论仅供其表达个人看法,并不代表农机新闻立场。