1 核心结构原理与技术演进
现代大马力拖拉机转向系统已从传统机械结构进化为机电液一体化智能平台,其技术突破主要集中在传动机构、控制算法和能源效率三大领域。
1.1 主流转向架构对比
类型 | 代表机型 | 工作原理 | 优势 | 局限 |
全液压转向(HSS) | 约翰迪尔8R系列 | 转向泵→优先阀→转向器→油缸 | 结构简单/维护成本低 | 路感缺失/能耗高 |
电液比例转向(EHPS) | 凯斯Magnum 380 | 电控单元→比例阀→流量放大油缸 | 转向力可调/响应快(80ms) | 液压依赖/故障率15% |
电动助力转向(EPS) | 克拉斯Xerion 5000 | 电机→减速机构→齿轮齿条 | 能效高(省油12%) | 扭矩受限(<35kN·m) |
线控转向(SBW) | 约翰迪尔Autonomous | 传感器→ECU→轮毂电机 | 无机械连接/支持无人作业 | 冗余设计成本高30% |
1.2 关键部件技术突破
转向泵革新:
变量叶片泵(博世力士乐):压力补偿阀使流量按需供给,比齿轮泵节能40%
双泵合流系统(ZF专利):主泵故障时备用泵0.3秒内接管,保障连续作业
执行机构升级:
双作用油缸:活塞杆镀铬层厚0.15mm(国标0.08mm),耐腐蚀寿命超10,000小时
摆线马达(丹佛斯OMM系列):容积效率达95%,配合压力切断阀防过载
控制阀进化:
负载敏感阀:根据转向阻力动态调节压力,减少无效功耗30%
比例方向阀(贺德克):0-10V信号控制流量精度±2%,实现毫米级转向微调
2 智能化控制技术
转向系统智能化体现在感知-决策-执行全链条升级,核心在于多源数据融合与实时控制算法。
2.1 感知层技术创新
传感器类型 | 技术参数 | 功能价值 |
扭矩传感器 | 量程±200N·m/精度0.5% | 实时监测方向盘输入力矩 |
角度传感器 | 0-360°非接触式/分辨率0.1° | 精准识别转向轮偏角 |
压力传感器 | 0-25MPa/耐温-40~125℃ | 监控液压系统状态 |
毫米波雷达 | 探测距离150m/精度±2cm | 地形预瞄与障碍物识别 |
2.2 控制算法突破
自适应PID控制:
克拉斯CEMOS系统通过模糊规则库动态调整参数:
低速工况:增大比例系数(Kp=1.2)提升响应速度
高速工况:加强微分控制(Kd=0.8)抑制车身摆动
预瞄控制模型:
约翰迪尔ActiveSteer™融合:
北斗RTK定位(精度±2cm)
IMU姿态数据(100Hz采样)
农田数字地图
实现转向动作提前300ms触发,作业直线偏差<2.5cm
铰接转向稳定性算法:
凯斯Steiger 620 Quadtrac采用:
math
ω_{max} = \sqrt{\frac{μg}{R}}
其中μ为附着系数(0.4-0.7),g为重力加速度
动态限制铰接角度变化率,防止高速转向侧翻
3 前沿结构与特殊工况解决方案
针对大马力拖拉机重载、大转弯半径等需求,创新机械结构持续涌现。
3.1 四轮转向系统(4WS)
类型 | 工作原理 | 性能增益 | 典型应用 |
同相位转向 | 前后轮偏转方向一致 | 减小转弯半径35% | 果园狭窄空间作业 |
逆相位转向 | 前后轮偏转方向相反 | 提升高速稳定性 | 道路运输 |
独立电控转向 | 各轮独立控制偏角 | 实现蟹行/原地转向 | 坡地精准耕作 |
案例:
克拉斯Xerion 4000:四轮独立转向+履带复合底盘,实现12m长机身5.5m转弯半径
3.2 铰接转向强化设计
中央铰接点:
圆锥滚子轴承(TIMKEN):轴向承载达120kN
硬化处理销轴(HRC58-62):磨损寿命超15,000小时
液压缸双安全阀:
先导式溢流阀(设定压力28MPa)
双向液压锁:防止管路爆裂导致失控
3.3 极端工况应对方案
泥泞地面:
压力敏感转向:检测轮速差>15%时自动降低助力
滑移补偿:增加内侧轮制动力矩恢复循迹性
坡地作业:
重心补偿算法:IMU监测倾角>10°时限制转向速度
双泵冗余:主泵故障时辅助泵维持50%流量
4 技术瓶颈与创新方向
尽管技术持续进步,转向系统仍面临可靠性、成本及控制复杂度三重挑战。
4.1 关键技术瓶颈
问题领域 | 具体表现 | 技术根源 |
液压系统可靠性 | 阀芯卡滞(粉尘污染) | 油液清洁度仅NAS 9级 |
电控系统容错 | 单点失效导致失控 | 冗余设计不足 |
大扭矩传递 | EPS最大支持35kN·m | 永磁电机功率密度限制 |
成本控制 | 4WS系统溢价40% | 高精度传感器占比成本60% |
4.2 创新解决方案
耐污染液压系统:
自清洁滤芯(唐纳森专利):集成离心预滤+纸质精滤
IP69K级密封(SKF):旋转轴封耐受100MPa高压冲洗
三重冗余电控架构:
约翰迪尔Autonomous采用:
主控:Xilinx Zynq UltraScale+ MPSoC
备份:NXP S32G处理器
机械应急:电磁离合器接合齿条
混合动力转向:
电液复合系统(博世Rexroth):
常规工况:电机驱动(节能30%)
峰值需求:液压助力(瞬时扭矩倍增)
超级电容储能:制动能量回收供转向用
5 未来发展趋势
转向系统正向全线控化、多功能集成与智能网联三大方向演进。
5.1 技术路线图
阶段 | 核心技术 | 性能目标 | 产业化进度 |
2025-2027 | 冗余线控转向 | 故障率<0.1%/千小时 | 约翰迪尔量产 |
2028-2030 | 轮毂电机四轮转向 | 原地转向/蟹行模式 | 克拉斯原型测试 |
2030+ | 自主决策转向 | AI路径规划响应<50ms | 高校实验室阶段 |
5.2 创新融合方向
农具协同转向:
CLAAS CEMOS系统实现:
犁具耕作角度自动补偿
播种机接行偏差<2cm
通过ISOBUS协议共享转向数据
新能源底盘适配:
氢能拖拉机:储氢罐布局限制传统转向柱
轮边驱动:取消中央传动轴释放空间
数字孪生运维:
潍柴智慧云平台实现:
转向油温实时监测(精度±1℃)
密封件磨损预测(误差<5%)
预防性维护建议生成
结论:智能转向重构作业范式
大马力拖拉机转向系统的进化史,本质是机械可靠性、控制精确性与能源效率的持续博弈:
机械层面:从齿轮齿条到全液压,再到线控转向,传动链简化使故障点减少60%
控制层面:北斗RTK+IMU+AI算法的融合,使作业精度进入厘米时代
能源层面:电动助力与能量回收技术,推动转向能耗降低40%
未来竞争焦点将集中在:
失效安全设计:三重冗余架构成本压缩至整机5%以内
轮毂电机集成:解决大扭矩输出与紧凑布局的矛盾
农业AIOS系统:转向数据成为农田数字孪生体核心参数
正如德国农业协会(DLG)报告所言:“转向系统的智能化程度,已成为衡量现代农业装备代际差异的分水岭”。当转向动作从人力操纵进化为自主决策,拖拉机正从“牵引工具”蜕变为真正的“田野机器人”。
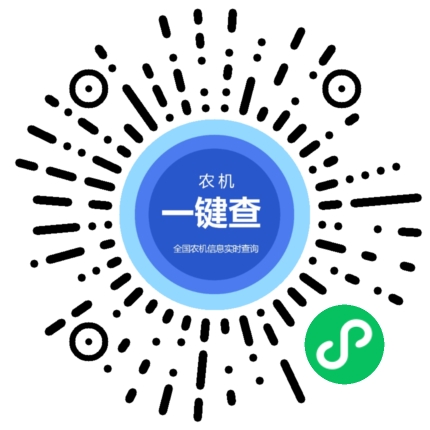
小程序扫码观看
更多农机资讯尽在农机一键查
版权声明:本文仅代表作者观点,不代表农机新闻网立场。 本文为分享行业信息所用,如需转载,请联系原作者。
网友评论仅供其表达个人看法,并不代表农机新闻立场。