1 HMCVT的技术原理与结构组成
液压机械无级变速器(Hydro-mechanical Continuously Variable Transmission, HMCVT)作为当代高端拖拉机的核心技术,彻底改变了传统农业机械的动力传输方式。这种革命性的传动系统通过行星齿轮机构将发动机动力智能分流为两条路径:液压功率流和机械功率流,最终在汇流排实现动力合成与无级调速。这种设计理念融合了液压传动的无级调速优势与机械传动的高效特性,解决了传统拖拉机在复杂工况下面临的动力中断与效率低下的问题。
1.1 核心结构解析
液压传动单元:由变量泵和定量马达(或双变量泵马达)组成,通过改变变量泵的斜盘倾角实现液压油流量和流向的精确控制。这一子系统主要负责速度调节功能,使拖拉机能够根据作业需求实现平滑的速度变化。在静液压传动(HST)模式下,系统可实现0速起步,为拖拉机提供极佳的操控性和低速作业精度。
机械传动单元:由行星齿轮机构、多片湿式离合器和齿轮组构成,负责高效传递大部分发动机功率(通常可达70-85%)。机械传动路径特别适合高速运输工况,此时传动效率可接近纯机械变速箱水平(约0.85以上)。
智能控制系统:作为HMCVT的“大脑”,该系统由多传感器网络(转速传感器、压力传感器、位置传感器等)、电子控制单元(TCU)和电液比例阀组成。系统实时采集发动机转速、车速、负载扭矩等参数,通过自适应算法(如双模糊PID控制)动态调节泵排量和离合器压力,实现发动机工况点与负载需求的最优匹配。
1.2 工作模式与功率流路径
HMCVT的精妙之处在于其能够根据工况需求在液压机械传动(HMT)和纯静液压传动(HST)两种模式间智能切换:
低速高扭矩工况(如开沟、重载起步):系统主要运行在HST模式,液压功率流占主导地位(可达总功率的70%)。此时变量泵大角度偏转,提供最大液压扭矩输出,实现低速高牵引力特性。在新疆大型农场的实际应用中,配备HMCVT的麦赛福格森3404拖拉机实现了0速平稳起步,在犁耕作业中表现出色。
中高速工况(如田间转移、道路运输):系统切换至HMT模式,机械功率流占比提升至80%以上,液压功率流逐渐减小至10-20%。这种模式充分发挥了机械传动的高效特性,显著降低油耗。当车速达到设定最高值时,TCU会将液压分流功率调定在0值附近,使变速器工作在纯机械工作状态,传动效率可达0.93以上。
模式切换过程:HMCVT通过多区段设计(通常3-5个)实现全域无级变速。在每个区段内,系统通过调节液压单元排量实现无级变速;在区段切换点,TCU控制湿式离合器在功率重叠状态下完成换段(约0.2-0.5秒),确保动力不中断。
表:HMCVT变速箱工作模式特性对比
工作模式 | 功率流分配 | 适用工况 | 传动效率 | 典型车速范围 |
HST模式 | 液压流70%-机械流30% | 低速重载作业(犁耕、爬坡) | 0.65-0.75 | 0-8 km/h |
HMT模式 | 液压流10-20%-机械流80-90% | 中高速作业(播种、运输) | 0.85-0.93 | 8-50 km/h |
纯机械模式 | 液压流<5%-机械流>95% | 高速运输 | >0.93 | >40 km/h |
2 性能优势与作业效能提升
HMCVT技术之所以成为高端拖拉机的标志性配置,源于其革命性的性能优势。这种传动系统不仅大幅提升了燃油经济性,还显著改善了作业效率与操作舒适度,为现代化精准农业提供了技术支撑。
2.1 燃油经济性与动力性能突破
发动机工况优化:HMCVT通过连续无级变速特性,使发动机始终稳定在最佳工作区间(通常为经济油耗区或最大功率区)。根据德国农业协会(DLG)的测试数据,相比传统动力换挡变速箱(PowerShift),HMCVT在犁耕、收获和运输三种典型工况下可实现9%-20% 的节油效果。江苏大学2022年的研究进一步证实,搭载油电混合动力与HMCVT的复合系统在犁耕工况下油耗仅为2.72L,比同级动力换挡拖拉机降低18%。
动力响应提升:HMCVT消除了传统变速箱的动力中断问题,在负载波动剧烈的工况下(如土壤硬度不均地块),系统通过液压支路的快速响应能力(毫秒级)维持车速稳定。采用滑转率-阻力区间划分法的调速控制策略可将驱动轮滑转率约束在容许区间内(通常15%-25%),使拖拉机车速和加速度分别由5.06 km/h和0.05 m/s²提升至5.3 km/h和0.15 m/s²,大幅提升了生产效率和复杂地形适应性。
2.2 作业效率与操作舒适性飞跃
作业效率提升:HMCVT实现了无级调速与速度精确控制(±0.1 km/h),特别适合对速度敏感的作业如精密播种、变量施肥等。实际应用表明,在新疆大型农场中,配备HMCVT的拖拉机播种作业效率比传统动力换挡机型提高25%以上,且播种均匀度显著改善。
操作革命:传统拖拉机操作中频繁的离合器操作和换挡决策对驾驶员造成巨大体能消耗。HMCVT通过单杆操纵和预设作业模式(如犁地模式、运输模式)极大简化了操作流程。约翰迪尔6R系列搭载的HMCVT更实现了与自动驾驶模块的深度集成,通过CAN总线接口接收导航指令,实现无人化精准作业。
2.3 系统可靠性与适应性优势
冲击载荷降低:液压油液的阻尼特性有效吸收了发动机扭矩波动和地面冲击载荷,传动系动载降低达40%。这一特性显著延长了传动系统部件寿命,尤其在中国东北等高强度作业环境中,HMCVT拖拉机的大修周期比传统机型延长2000小时以上5。
复杂环境适应性:HMCVT在泥泞、坡地等复杂地形中展现出卓越的适应性。其独特的低速大扭矩特性(0速时输出最大扭矩)使拖拉机能够轻松应对深泥泞地块起步和重载爬坡等挑战工况。在欧洲阿尔卑斯山地区坡地农场,配备HMCVT的福格森拖拉机在30°以上坡度作业时仍能保持稳定车速,作业效率比传统机型提高30%。
表:HMCVT与传统变速箱性能参数对比
性能指标 | HMCVT变速箱 | 动力换挡变速箱 | 手动变速箱 | 提升幅度 |
传动效率峰值 | 0.93 | 0.85 | 0.82 | +9.4% |
燃油经济性 | 降低15-25% | 降低8-12% | 基准 | +9-20% |
换挡动力中断 | 无 | 0.2-0.5秒 | 1-2秒 | 100%消除 |
速度控制精度 | ±0.1 km/h | ±0.5 km/h | ±1.0 km/h | 提高5-10倍 |
操作复杂度 | 单杆操作 | 自动换挡 | 手动离合+换挡 | 降低70% |
制造成本 | 高(溢价30%) | 中等 | 低 | - |
3 关键技术突破与创新设计
HMCVT系统的卓越性能源于多项关键技术的突破性创新。这些技术涵盖了行星排设计、湿式离合器、智能控制算法等核心领域,共同构成了HMCVT的技术壁垒。
3.1 行星排与湿式离合器创新
双排汇流行星机构:南京农业大学研发的双排行星齿轮汇流结构采用“前圈后架”刚性联接设计,配合滑动轴承支撑结构,有效解决了双排行星齿轮在变速箱内部的支撑、润滑及滚针轴承冷却问题5。这种设计不仅实现了功率的高效合成,还通过传动比优化分配使液压功率流占比降至15%-30%,大幅提升了系统综合效率。
湿式多片制动器:专利技术(202021025383)采用交错油孔设计的渐开线花键,在主动毂与制动毂齿根部位开设多个交叉排布的油孔,既满足了摩擦片与对偶钢片的冷却润滑需求,又避免了应力集中问题3。制动毂内花键处的卡簧槽设计实现了对摩擦片组的轴向精准定位,结合O型密封圈的优化布局,确保了制动器的密封性和长期稳定性3。
3.2 智能控制算法突破
滑转率-阻力区间划分法:中国农业大学开发的这一创新控制策略通过对滑转率区间划分确定控制优先级,通过对作业阻力范围划分确定最佳传动模式。当驱动轮滑转率处于容许区间(15%-25%)时,优先保障生产效率;当滑转率超过最大容许值(如30%)时,则优先保障通过性4。基于前馈补偿的滑模控制算法有效克服了油压波动对液压泵排量调节精度的不利影响,使系统在负载剧烈波动时仍能保持精准的速度控制4。
模式切换动力学控制:针对HMCVT模式切换过程中的动力中断风险,重庆大学提出回流式功率循环设计(PCHMCVT),通过行星机构的耦合与泵-马达液压系统功能转换,将液压回流传动与分流传动有机结合10。这种设计使系统兼具液力与液压传动双重优势,实现了全时全程无级调速和低速增扭特性,速比范围拓宽至传统HMCVT的1.5倍。
3.3 混合动力集成创新
油电混动HMCVT系统:江苏大学开发的创新架构将油电混合动力与HMCVT无缝集成,提出了经济性速比控制策略、基于规则的工作模式划分策略和基于自适应等效因子的燃油消耗最小功率分配策略68。该系统在犁耕、收获和运输三种工况下的油耗仿真值(2.59、6.56和1.69L)与试验值(2.72、6.80和1.77L)误差不超过5%,验证了模型可靠性。
多模式功率分配:混动HMCVT系统支持纯电驱动、串联混动、并联混动和发动机直驱四种工作模式。在低速轻载工况(如田间转场)下,系统可切换至纯电模式,实现零排放和低噪音作业;在高负荷犁耕工况下,发动机与电机并联驱动,提供最大扭矩输出6。玉柴IE-Power系列采用串联式混动方案(柴油发动机+发电机+电机+2档AMT),结构简单且成本较低,特别适合频繁启停的轻载作业。
4 产业化应用与市场格局
HMCVT技术已从实验室走向大规模产业化,全球主要农机巨头纷纷推出各具特色的HMCVT产品,形成多元化技术路线并存的竞争格局。
4.1 国际领先企业技术路线
约翰迪尔(John Deere):作为HMCVT技术领导者,其eAutoPower™ 系统采用并联式混动架构,将传统HMCVT的静压传动单元替换为电驱模块,通过行星机构实现机电动力汇流。2019年汉诺威农机展推出的8R410拖拉机虽未引入中国,但在北美市场展示了纯电作业模式的潜力,可实现夜间低噪音作业。
采埃孚(ZF):其ECCOM系列CVT代表机械制造精度的巅峰,采用多层行星架嵌套技术和多组多片湿式离合器配合的动力换挡技术,实现了无冲击的平稳换段17。采埃孚的独特优势在于其湿式离合器模块可承受高达450 N·m的扭矩冲击,使用寿命达10,000小时以上,远超行业平均水平。
克拉斯(CLAAS):2014年推出的CMATIC变速箱采用创新的三区段设计,通过优化行星排结构减少了40%的液压元件数量,在保持无级变速特性的同时显著提升了可靠性1。克拉斯HMCVT的独特之处在于其液压系统冗余设计,即使单泵故障仍能维持50%的液压动力输出,大幅提升了系统鲁棒性。
4.2 国内厂商技术突破
潍柴雷沃:开发的200-300马力级HMCVT通过行星排优化设计,传动效率达0.85以上,综合能耗降低15%1。其箱体采用中间支撑肋板和内嵌式冷却润滑油道,三角形加强筋设计显著减少轴承孔变形,在新疆棉田等高负荷工况下表现出色17。
中国一拖:东方红系列拖拉机搭载的HMCVT采用双模糊PID控制算法,在阶跃负载下缩短转速调整时间20%以上7。其独特的前馈控制策略通过Matlab仿真验证,使各区段传动效率均超过80%,调速范围覆盖0-50 km/h,适应犁耕、播种等多种作业场景。
表:全球主流HMCVT产品技术参数对比
厂商/型号 | 最大输入扭矩(N·m) | 功率范围(hp) | 速比范围 | 工作区段 | 控制算法 | 特色技术 |
ZF ECCOM | 1100 | 180-450 | 0.42-3.05 | 4区段 | 自适应PID | 多层行星架嵌套 |
John Deere eAutoPower | 950 | 210-410 | 0.38-2.98 | 3区段 | 神经网络控制 | 电驱静压单元 |
CLAAS CMATIC | 1050 | 240-480 | 0.40-3.10 | 3区段 | 模糊控制 | 液压冗余设计 |
潍柴雷沃HMCVT | 850 | 200-300 | 0.45-2.85 | 3区段 | 双模糊PID | 内嵌式冷却油道 |
中国一拖DFHMCVT | 780 | 180-280 | 0.48-2.75 | 3区段 | 前馈PID | 加强肋板结构 |
5 技术挑战与未来创新方向
尽管HMCVT技术已取得显著进步,但在产业化和大规模应用过程中仍面临多重挑战,这些挑战也指明了未来技术创新的方向。
5.1 当前技术瓶颈
制造成本高企:高端HMCVT系统成本比传统动力换挡变速箱高30%以上,主要源于精密液压部件(如轴向柱塞变量泵)和多片湿式离合器模块的昂贵成本。例如,采埃孚ECCOM系列CVT的液压单元由德国博世力士乐独家供应,单套价格超过2万美元,占变速箱总成本的40%。
液压系统限制:国产HMCVT普遍面临液压元件泄漏和压力波动问题。在持续高负荷工况下,液压油温可能超过100℃,导致粘度下降和内泄增加,效率降低15%-20%49。国内企业的液压部件主要依赖进口,如潍柴雷沃HMCVT的液压单元采购自德国林德液压,成本占比高达35%。
控制算法复杂度:HMCVT需要同时协调变量泵排量、离合器压力和发动机节气门,形成多变量、强耦合的复杂控制问题。尤其在模式切换过程中,液压机械模式与静液压模式的转换易引发动力波动,国内系统的切换冲击度比采埃孚产品高30%,影响操作舒适性。
5.2 未来创新方向
混合动力深度集成:油电混动HMCVT成为下一代技术制高点,重点突破功率分配策略优化和机电耦合动力学问题。约翰迪尔正在开发的eAutoPower+ 系统将电机功率提升至100kW,支持30分钟纯电作业,特别适合温室等封闭环境1。国内科研团队提出的基于自适应等效因子的燃油消耗最小功率分配策略,在犁耕工况下实现了2.72L的油耗,比传统HMCVT进一步降低12%。
智能化升级:融合物联网和大数据技术的智能HMCVT成为研发热点。主要方向包括:基于数字孪生的变速箱健康管理系统、基于深度学习的自适应换挡策略、基于北斗定位的预见性速度控制等79。约翰迪尔正在测试的AI耕作算法能根据作物密度实时调整车速,在玉米收获作业中减少籽粒损失率达15%。
材料与结构创新:轻量化设计和热管理系统优化成为提升可靠性的关键。碳纤维复合材料在制动毂和行星架上的应用可减重30%;纳米陶瓷涂层摩擦片使离合器耐热温度提升至350℃;嵌入式微通道冷却技术使湿式离合器散热效率提高40%37。重庆大学开发的回流式液压机械无级传动(PCHMCVT)通过功率循环拓宽速比范围至传统系统的1.5倍,为低速大扭矩作业提供创新解决方案。
6 中国企业的突破路径
面对国际巨头的技术壁垒,中国农机企业需要制定科学的突围策略,在核心技术创新与产业化应用上走出一条中国特色发展道路。
差异化技术路线:发挥国内电控系统和电机驱动领域优势,重点突破混动ECVT技术路线16。潍柴雷沃正在开发的电驱静压单元以永磁同步电机替代传统液压泵,不仅规避了高精度液压元件制造难题,还将响应速度提升至毫秒级。玉柴IE-Power系列采用串联式混动架构(柴油机+发电机+电机+2档AMT),结构简单且成本较低,已在多家国内二线主机厂推广应用。
模块化平台开发:建立分级配套体系,对高端液压元件(如轴向柱塞泵)采取国际采购策略,同时集中攻克湿式离合器模块和行星排总成的国产化。中国一拖开发的HMCVT平台化架构通过标准化接口支持不同功率段需求,离合器模块和行星排实现了85%的通用化率,大幅降低制造成本和维护复杂度。
产学研深度融合:南京农业大学开发的双排行星汇流结构通过滑动轴承支撑方案解决了行星齿轮润滑与冷却难题;江苏大学提出的油电混动HMCVT系统在犁耕、收获和运输工况下实现9%-20%的节油效果;中国农业大学的滑转率-阻力区间划分法将作业效率提升12%4。这些创新成果为国产HMCVT技术突破提供了坚实支撑。
智能化软件赋能:集中资源开发具有自主知识产权的HMCVT控制算法库和数字孪生平台。潍柴雷沃的智能调速系统通过深度学习驾驶员操作习惯,自动优化换挡策略,使新手驾驶员也能达到熟练驾驶员的操作效率。一拖集团开发的远程故障诊断系统能提前500小时预测离合器磨损状态,将意外停机率降低60%。
结论:效率革命与智能融合
HMCVT技术正引领全球高端拖拉机传动系统的深刻变革,从最初的液压-机械复合传动向油电混动和智能网联方向快速演进。这项技术成功解决了农业机械在复杂多变工况下面临的动力连续性、燃油经济性和操作舒适性三大核心问题,成为现代农业装备升级的核心驱动力。
未来五年将是HMCVT技术发展的关键窗口期,主要呈现三大趋势:混动化、智能化和平台化。混动化聚焦于电驱动单元与液压机械传动的深度耦合,实现能量利用率再提升20%;智能化体现在基于物联网的自适应控制算法,使变速箱具备“学习”作业环境的能力;平台化则是通过模块设计满足不同功率段和作业场景需求,降低制造成本30%以上。
中国农机工业虽然起步较晚,但在国家战略支持与市场需求的双重驱动下,通过差异化技术路线、模块化平台开发和产学研深度融合三大策略,有望在混动ECVT等新兴赛道实现弯道超车。随着潍柴、一拖等龙头企业持续投入,中国HMCVT技术将在2030年前完成从“跟跑”到“并跑”的关键转型,为全球农业机械化贡献中国智慧。
正如一位资深农机工程师所言:“土地不会变得更柔软,但我们可以让钢铁更智慧。”HMCVT技术正是这一理念的最佳诠释——它将持续推动农业动力传动系统的效率革命,为人类应对粮食安全挑战提供关键技术支撑。
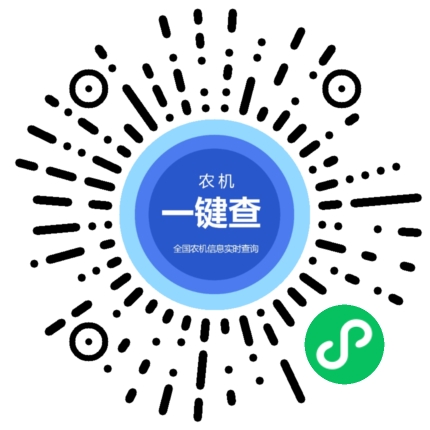
小程序扫码观看
更多农机资讯尽在农机一键查
版权声明:本文仅代表作者观点,不代表农机新闻网立场。 本文为分享行业信息所用,如需转载,请联系原作者。
网友评论仅供其表达个人看法,并不代表农机新闻立场。