1 大马力拖拉机高端化转型趋势与售后市场滞后性
中国农机产业正经历从“规模扩张”向技术密集型转型的关键阶段。2025年,国产200马力以上拖拉机市场规模已达126亿元,核心部件国产化率从不足40%向50%突破,一拖股份、潍柴雷沃等龙头企业加速推进无级变速(CVT)、动力换挡、混合动力等高端智能拖拉机的研发与产业化。这一转型的底层逻辑是农业规模化经营的需求驱动——东北、新疆等粮食主产区大型农场深松作业深度要求达35cm以上,传统机械传动拖拉机已无法满足高效低耗需求。
技术升级的核心标志是电液控制替代纯机械结构。以一机集团突破的20400N·m大扭矩前驱动桥为例,其采用模块化设计理念,动态载荷能力提升17%,但内部集成了压力传感单元、电子控制阀组等精密部件。同样,一拖股份开发的混合动力拖拉机配备双电机耦合系统,能量管理算法复杂度呈指数级增长。这些技术进步虽显著提升作业效率(如犁耕工况油耗降低30%),却也导致故障诊断从传统的“经验判断”转向多源数据分析,维修人员需掌握液压、电子、算法等跨学科知识。
然而,售后服务体系与高端化进程呈现显著断层。据新泰市调研数据,全市农机维修网点从145个锐减至48个,具备电控系统维修能力的网点不足20%,且集中分布在城区4。这种滞后性直接反映在用户端:2025年湖北农户购买的6万元拖拉机因变速箱控制模块故障瘫痪两月,厂家竟以“小马拉大犁”为由推诿责任,最终诉诸法院才实现退车。更深层的矛盾在于,高端机型的三包期故障率虽低于传统机型,但单次维修成本增加200%,且平均等待配件时间长达14天。
表:高端大马力拖拉机与传统机型售后需求对比
维度 | 传统机械传动拖拉机 | 高端智能拖拉机(200+马力) |
典型故障类型 | 齿轮磨损、离合器片烧蚀 | 传感器失效、控制算法失准、液压阀卡滞 |
维修技术需求 | 机械拆装技能 | 电控诊断仪使用、数据流分析、软件刷写 |
平均修复时间 | 2-3小时 | 1-3天(含诊断与配件调配) |
单次维修成本 | 300-800元 | 2000-5000元 |
配件可获得性 | 80%网点常备 | 需省仓调货(覆盖率<30%) |
这种断层本质上暴露了产业升级的系统性失衡:企业资源向研发与销售倾斜,而售后被视作“成本中心”。某头部企业财报显示,其研发投入年增15%,但售后服务预算占比连续三年停滞在2.3%。当钢铁巨兽驰骋在黑土地上时,支撑其持续运转的服务网络却仍在蹒跚学步。
2 高端化引发的售后市场多维挑战
高端大马力拖拉机的技术跃迁正将售后服务体系推向多维压力场,具体表现在技术门槛、服务成本、配件供应、人才储备等环节的连锁反应。
2.1 技术门槛的跃升与能力断层
传统机械维修的“锤子扳手”模式在高端机型面前彻底失效。以动力换挡变速箱为例,其故障诊断需连接专用诊断仪读取控制单元数据流,分析压力传感器、转速传感器的协同逻辑。吉林某农场主购置的60马力拖拉机频繁出现动力中断,当地维修工耗时三天未能排除故障,最终厂家技术团队通过远程分析CAN总线报文发现是挡位指令信号冲突。更严峻的是,部分企业为保护知识产权,对控制系统设置技术壁垒——湖北代先生的芬沃拖拉机故障码需厂家专用设备解码,普通服务站束手无策。这种技术垄断使80%的县域维修网点被迫放弃高端机型服务,形成“修不了→用户流失→技能退化”的恶性循环。
2.2 服务成本高企与盈利困境
高端农机售后服务正陷入 “三重成本挤压” 的困局:
人力成本激增:具备电控维修能力的技师年薪达12-15万元,是传统维修工的2倍。一家年销万台拖拉机的企业若配备80人技术服务团队,仅工资差旅年支出就超千万元
配件库存压力:CVT变速箱控制模块单价超6000元,但故障率不足1%。为保障及时性,省级仓库需常备20个以上,占用资金逾12万元。
服务半径制约:高端机型用户分散,单次现场服务往返常超200公里。新疆某服务站为修复一台260马力拖拉机液压系统,派遣两名技师驱车14小时,仅油费过路费就消耗超过1500元
更严峻的是,这些成本难以向用户转嫁。调研显示,75%的农户拒绝支付超过设备价3%的维修费,而高端机型单次系统维修实际成本常达设备价的5%-8%。企业被迫内部消化成本,售后服务部门普遍沦为利润黑洞。
2.3 配件供应断层与寿命周期管理缺失
高端农机配件供应呈现 “两极化断裂” :
停产即断供:山东芬沃等企业产品迭代加速,老机型停产后核心配件即停产。湖北用户购买的拖拉机使用两月后故障,竟被告知“型号已淘汰,无配件储备”
进口依赖症:无级变速器比例阀、高压共轨喷油器等关键件进口占比超60%。某企业服务总监透露,德国博世液压阀断供时,200台大马力拖拉机被迫停摆40天.
其根源在于全寿命周期管理缺位。行业通行做法是整机停产后配件供应维持3年,但大马力拖拉机平均使用年限达10年,导致后期“无件可换”。新疆兵团一台进口CVT拖拉机因控制主板损坏,更换费用高达8万元,相当于新机价格的15%。
2.4 专业人才缺口与服务网络萎缩
农机维修行业面临 “后继无人” 的危机:
人员结构老化:新泰市维修从业者中45岁以上占比达67%,年轻技工更倾向汽车维修行业4
培训体系脱节:职业院校农机专业多聚焦机械原理,电控技术课程占比不足20%6
服务半径过大:单网点平均覆盖半径达70公里,农户紧急故障需等待6小时以上
江西高安种粮大户丁旦的遭遇颇具代表性:其农机队拥有31台先进设备,但2024年3名“95后”技师离职转行,因“修农机不如修轿车体面”。人才断档进一步加剧服务网络萎缩,形成恶性循环。
表:大马力拖拉机售后服务成本结构分析(以年销万台企业为例)
成本项 | 传统机型 | 高端机型 | 增幅 | 痛点解析 |
人力成本 | 480万元/年 | 1100万元/年 | 129% | 电控技师薪资高、培训投入大 |
配件库存 | 800万元 | 2200万元 | 175% | 精密件价格高、周转率低 |
现场服务 | 200元/次 | 850元/次 | 325% | 远程支援无效时长途差旅 |
技术支持 | 60万元(软件授权) | 300万元(诊断平台) | 400% | 专用解码设备、远程系统费用 |
综合占比 | 销售额的4.2% | 销售额的9.8% | 133% | 超出农户支付意愿阈值 |
3 行业破局:创新服务模式与技术赋能
面对系统性挑战,领先企业正通过技术重构、生态协同、政策借力三轨并行的策略开辟破局路径。
3.1 技术重构:模块化设计与智能运维
硬件模块化:一机集团前驱动桥采用分段式壳体设计,齿轮组与电控单元独立封装。当传感器故障时,只需更换30×20cm的模块组件,工时从8小时压缩至1.5小时,成本降低70%
预测性维护:一拖股份在动力换挡拖拉机部署 “北斗+物联网”终端,实时监测变速箱油温、压力等参数。当数据异常时自动预警,故障修复时间平均缩短64%。江苏试点显示,该技术使大修间隔延长至1800小时,较传统机型提升50%
AR远程支援:雷沃重工为服务站配备增强现实眼镜,技师现场扫描故障码后,专家团队可远程标注拆解步骤。黑龙江测试表明,复杂液压故障修复效率提升40%,新手技师培养周期缩短60%
3.2 服务生态重构:从单点突破到网络协同
配件联合储备池:山东五县试点 “1小时配件圈” ,10家服务站共建共享中心仓库,关键件库存下降35%但保障率提升至90%。通过区块链技术实现配件溯源,杜绝仿冒件流通
跨界技术联盟:潍柴动力联合华为开发农机鸿蒙操作系统,向第三方维修商开放诊断接口。维修点支付年费3万元即可获得全协议解码能力,较购买原厂设备成本降低85%
“滴滴式”服务众包:沃得农机APP上线“铁牛快修”功能,认证技师可接单就近服务。新疆用户呼叫后平均47分钟响应,较传统模式提速3倍,技师月增收超4000元
3.3 政策借力:基础设施与标准升级
高标准机库建设:江西丰城试点农机公寓项目,政府提供50%建设补贴。配备恒温仓库的机库使精密部件存储寿命延长2倍,露天存放导致的故障率下降27%
补贴机制改革:江苏省将售后评级纳入购置补贴考核:获五星级服务认证的企业可追加3%补贴额度,倒逼企业投入服务体系建设
4 未来之路:构建韧性服务生态
大马力拖拉机高端化不可逆转,售后市场需向技术密集型、数据驱动型、共享经济型三态融合的新生态进化。
4.1 智能化服务基座建设
数字孪生预诊:基于历史故障库构建 “虚拟拖拉机”模型,在液压系统温升异常时自动匹配相似案例,推荐处置方案。玉柴IE-POWER系统实测显示,早期故障识别率达92%
柔性配件供应链:3D打印应急配件成破局利器。山东试点服务站配备金属打印机,变速箱外壳等非承重件现场制作,应急响应时间缩短至4小时
4.2 基础设施共享机制
多功能能源站:借鉴新能源汽车换电站模式,黑龙江农垦建设 “光储修一体化”站点。白天光伏发电支持维修设备运转,夜间为电池充电,同时作为配件前置仓。单站服务半径50公里,运维成本降低60%
土地流转配套:规模化经营推动服务集约化。江西万年县土地流转率达78%后,农机合作社可统一安排保养计划,服务成本下降35%
4.3 产业协同新范式
“制造+服务”金融创新:迪尔中国推出 “小时保障计划” ,农户按作业小时支付全包服务费(含配件、人工),企业通过保险分摊风险。试点区域用户接受度达72%
再制造产业链激活:河北建立旧件逆向物流体系,废旧变速箱经再制造后性能恢复90%,成本仅新品40%。圣和农机借此将200马力以上旋耕机齿轮箱供货周期缩短至7天
5 结语:在变革的土壤中深耕服务价值
大马力拖拉机的高端化浪潮正将中国农机产业推向历史性转折点。当价值百万的无级变速拖拉机驰骋在东北黑土地上时,其背后是技术跃迁与服务短板的激烈碰撞。从湖北农户因“无件可修”愤然起诉,到一机集团前驱动桥国产化突破,再到圣和农机特高箱旋耕机的创新突围,这些片段共同勾勒出产业升级的阵痛与希望。
解决售后困局的钥匙在于重构价值认知:售后服务不应是“成本黑洞”,而是品牌护城河与持续利润源。正如汽车行业已验证的规律——成熟市场中后市场利润占比可达总利润60%,农机行业的高端化转型必须伴随服务价值的重估。当潍柴开放诊断协议、沃得构建“滴滴式”服务网络时,我们看到的不仅是技术创新,更是产业协作范式的革命。
未来已来的信号愈发清晰:在江苏的“五星服务认证”政策中,在黑龙江的光储修一体化电站里,在职业院校新开设的电控诊断课程中,一种技术普惠、资源共享、责任共担的新服务生态正在生长46。这不仅是应对挑战的权宜之计,更是中国农机产业从规模扩张迈向高质量可持续发展的必由之路。当钢铁巨兽与智慧服务网络共舞之时,中国农业现代化的根基将更加坚实。
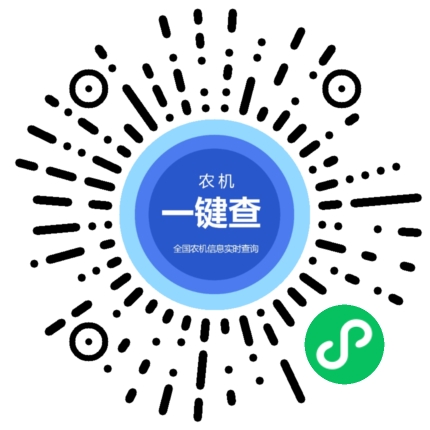
小程序扫码观看
更多农机资讯尽在农机一键查
版权声明:本文仅代表作者观点,不代表农机新闻网立场。 本文为分享行业信息所用,如需转载,请联系原作者。
网友评论仅供其表达个人看法,并不代表农机新闻立场。