动力换挡变速箱作为现代拖拉机技术的核心部件,其性能直接关系到农业机械的作业效率、操作舒适性以及动力输出的稳定性。然而,国产拖拉机行业在这一领域长期受制于技术瓶颈和供应链依赖,成为制约高端农机发展的“锥心之痛”。本文将从技术原理、核心难点、产业现状及未来突破方向等方面,系统分析拖拉机动力换挡变速箱的重点及难点。
一、动力换挡变速箱的技术重点
动力连续性控制
动力换挡的核心在于换挡过程中动力不中断,这对变速箱的同步器、离合器及控制系统提出了极高要求。传统手动变速箱通过离合器分离实现换挡,动力中断会导致发动机负载突变,尤其在重载作业(如耕地)时易造成发动机磨损和效率下降。动力换挡技术需通过湿式离合器组、电液控制系统和精准的换挡逻辑设计,确保动力输出的无缝衔接。例如,德国ZF公司的动力换挡变速箱通过多片湿式离合器的交替接合,实现动力流的连续切换。
智能化程序控制
动力换挡变速箱的控制系统需与拖拉机作业工况高度匹配。程序需实时采集发动机转速、负载、作业速度等参数,并通过电磁阀或电控单元(ECU)调整离合器的接合压力与换挡时序。技术难点在于如何在复杂多变的田间环境中(如泥泞、坡地)实现换挡逻辑的自适应优化。
核心零部件的设计与制造
湿式离合器:需采用耐高温、抗磨损的摩擦材料(如纸基摩擦片),其性能直接影响变速箱的寿命与可靠性。目前国产摩擦片在220马力以上拖拉机的适配中仍依赖进口。
液压系统:包括高压泵、控制阀和传感器,需在紧凑空间内实现高精度流量控制。国产液压元件在响应速度和稳定性上与国外产品存在差距。
高精度齿轮:动力换挡变速箱的齿轮需承受高频次冲击载荷,其加工精度和热处理工艺要求极高,国内在齿轮表面硬化技术和疲劳寿命测试方面仍需突破。
传动系组合:相比于约翰迪尔e23系列所谓全动力换挡变速箱来说,诸如采埃孚T7000系列动力换挡变速箱都是采用组合式的结构,及该变速箱由动力换挡部分、同步器换挡部分、爬行档部分和后桥四个部分组合而成,而约翰迪尔e23系列变速箱就是一个完整的动力换挡变速箱,没有后桥和其他部分。对于组合变速箱来说,单独开发一个部分或许技术难度没有高,但是组合在一起开发,并且要保证稳定的产品质量,这种难度值瞬间就爬升了不少。其中任何一个部分有问题,对于整个传动系来说造成的影响将是指数级的上升。所以这也就是为什么动力换挡变速箱的开发对于国内95%的主机厂来说都是一道迈不过去的坎。
二、技术难点与产业瓶颈
程序控制系统的技术壁垒
国内企业在动力换挡程序开发中面临两大难题:
动力连续性的算法优化:换挡过程中需精确控制离合器油压,避免因接合过快导致冲击,或过慢引发动力中断。控制算法的编写目前对于国内的相关企业来说都是地狱级的难度,之前我们没有开发过类似的算法,没有任何的经验可以参考,一套成熟稳定的换挡逻辑算法需要相关企业大量的作业数据和模式作为参考,只有在实际应用过程种不停的测试才能够真正完善。
带排转矩的抑制:湿式离合器分离时,摩擦片与隔板间的油膜剪切力会产生残余转矩(带排转矩),导致动力传递不完全切断。湿式多片离合器的分离和结合过程是都过了换挡变速箱控制算法的核心;离合器过早的离合将会导致变速箱挂双档,离合器过晚的结合将会导致变速箱脱档,对于重载作业的拖拉机来说,这两种情况都是不可接受的;唯有在离合器分离和结合过程实现完美的配合,在离合器分离的瞬间,另外一组离合器实现结合,真正实现在动力传递的过程中不中断,这才是动力换挡变速箱的核心所在。目前需通过改进摩擦片间隙设计和离合器充放油过程的精准控制,实现变速箱的完美柔和换挡。
核心零部件的进口依赖
国产动力换挡变速箱的供应链存在严重短板:
湿式纸基摩擦片:适配220马力以上拖拉机的摩擦片几乎全部依赖进口,国产材料在高温耐久性和摩擦系数稳定性上尚未达标3。
液压元件与传感器:高压泵、比例阀及角度传感器的国产化率不足30%,导致成本高企且供货周期不稳定。
电控系统:核心ECU模块多采用博世、采埃孚等外资品牌,国内在嵌入式软件开发和硬件集成能力上存在代际差距。
研发投入与人才短缺
动力换挡技术的研发周期长、成本高,单个项目投入可达数亿元,而国内农机头部企业(如一拖、福田雷沃)的年利润仅数千万至数亿元,难以支撑持续投入。此外,复合型人才(机械、电子、材料)的短缺进一步制约了技术创新。例如,湿式离合器的摩擦学优化需要材料科学与动力工程的跨学科协作,而国内高校在此领域的交叉培养体系尚未成熟4。
市场推广与用户接受度
目前国内动力换挡拖拉机年销量仅2000余台,不足市场总量的1%。高售价(比传统机型贵30%-50%)和用户认知不足是主要障碍。新疆、黑龙江等大规模农场虽为需求主力,但中小农户更倾向于价格低廉的手动挡机型。此外,国产动力换挡产品的故障率偏高(如跳挡、液压泄漏),进一步削弱了市场信心。
三、未来突破方向
技术路径的多元化探索
Hi-Lo动力换挡向全动力换挡升级:国内企业已掌握Hi-Lo(高低档切换)技术,下一步需攻克多速全动力换挡(如16速以上)的模块化设计,并逐步向无级变速(CVT)延伸。
新能源融合:电动或混合动力拖拉机可简化传动结构,利用电机直接驱动实现无级变速,规避传统变速箱的技术瓶颈。
产业链协同创新
跨行业技术移植:借鉴工程机械(如三一重工)和商用车(如中国重汽)的成熟经验,引入自动化生产线和智能检测技术,提升变速箱的制造精度。
国产替代加速:通过政策扶持(如《产业基础创新发展项目》)推动纸基摩擦片、高压液压阀等关键零部件的国产化,建立本土供应链生态。
智能化与可靠性提升
自动驾驶集成:将动力换挡控制系统与自动驾驶模块(如北斗导航)结合,实现换挡逻辑的实时优化。例如,根据地形坡度自动选择最佳挡位,减少人工干4。
故障预测与健康管理(PHM):通过传感器监测变速箱振动、温度等参数,结合大数据分析预判故障,降低维修成本。
四、结论
拖拉机动力换挡变速箱的突破不仅是技术问题,更是一场涉及产业链、政策支持和市场培育的系统性变革。当前国产企业的困境折射出中国高端装备制造业的普遍挑战——核心技术的自主化与产业链的韧性。未来,唯有通过跨行业协同、政策精准扶持(如分级补贴高端机型)以及企业持续创新,才能打破外资垄断,实现从“跟跑”到“并跑”的跨越。华为在通信领域的突围经验表明,唯有掌握核心技术,方能赢得市场话语权。农机行业亦需以此为契机,加速迈向智能化、绿色化的新赛道。
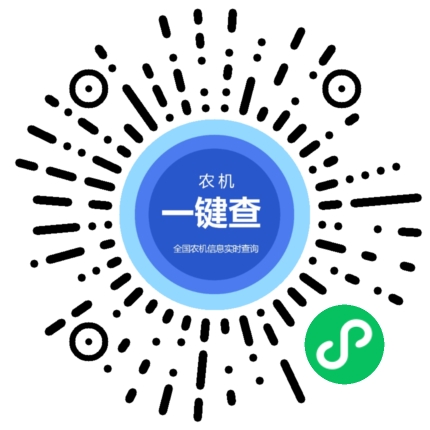
小程序扫码观看
更多农机资讯尽在农机一键查
版权声明:本文仅代表作者观点,不代表农机新闻网立场。 本文为分享行业信息所用,如需转载,请联系原作者。
网友评论仅供其表达个人看法,并不代表农机新闻立场。